
Allied Mineral Products Contains High Heat and IT Issues
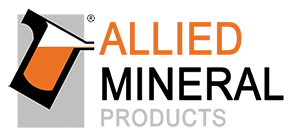
At a Glance
Challenges
- Global manufacturer requires reliable colocation services as disaster recovery location
- Time-intensive backups using significant bandwidth caused problems for international locations
- Impending move to the cloud to phase out aging servers
Benefits
- Excellent environment with presence on a secure grid and a strong fiber backbone
- Responsive and flexible Racksquared staff members also focused on long-term strategic upgrades
- Significant expertise in supporting customers moving technology resources to the cloud
By partnering with Racksquared, Allied is able to reduce the heat associated with a potential IT outage.
Focused on containing heat
Allied Mineral Products manufactures monolithic refractory ceramics that contain high heat. Its products are used anywhere extreme heat must be contained, including foundries, steel mills, car manufacturers, launch pads for spacecraft, and crematories. Allied’s products are also found closer to home – in the ovens at pizza restaurants and in the inserts for fireplaces purchased at home improvement stores. Based in Columbus, Ohio, the company operates 12 plants in the U.S., China, and several other countries, and it’s continuing to expand globally.
More than 10 years ago, Allied became one of Racksquared’s first customers when it colocated servers as part of its disaster recovery strategy.
“I remember when we drove our boxes over to Racksquared,” said Jeff Williams, Director of IT for Allied. “We appreciated that Racksquared had a great location and environment in downtown Columbus. It’s on the same power grid as a major hospital, so we knew it would receive top priority in case of an outage, and it has a high speed redundant fiber backbone.”
By colocating with Racksquared, Allied felt confident they could contain any problems arising from a disaster and get back on its feet quickly. With servers colocated at Racksquared, Allied believed that in the event of a disaster, they could recover their x86s and iSeries within their recovery time objective (less than 24 hours).
“If our servers go down, it would be very difficult for our manufacturing facilities to do business. They wouldn’t be able to create sales orders, print pick lists, invoice customers, or access administrative materials.” said Jeff. “So, a reliable solution is extremely important to us. With Racksquared, we see the reliability and uptime that our business needs.
“We are really impressed with the friendliness, knowledge and responsiveness of Racksquared’s staff. We’ve always been able to get on the phone with someone to walk us through any issues.”
-Jeff Williams, Director of IT at Allied Mineral Products
Ready to put out any fires
Racksquared’s Columbus location has been ideal. Early on, Allied staff members would sometimes stop by the facility to pick up or drop off tapes, and they could work with Racksquared staff in person when they wanted to.
Alternatively, when it’s not convenient to stop by, Racksquared is ready with remote hands services to take care of any quick requests — like switching a tape or checking a light. This kind of flexibility and responsiveness from Racksquared is important to Allied
“With some other providers, we’ve had the experience of opening a ticket about an issue and then not hearing from them for a long time. That doesn’t happen with Racksquared,” said Jeff.
In addition to providing great support, Racksquared has also played a significant role in delivering improved levels of service. It has added VPN connections to a number of Allied’s locations so they can immediately connect to servers in the event of a disaster. Racksquared also recently coordinated the installation of dark fiber between its data center and Allied’s building.
“Our backups had gotten so big that they were taking almost 20 hours to complete and gobbling up all of our bandwidth. That led to our international locations experiencing problems connecting to our corporate headquarters,” said Jeff. “With the dark fiber installed, we’ve reduced our backup time to just 2-3 hours. It’s made a world of difference.”
Warming up to move to the cloud
Looking ahead, Allied is working to phase out its aging on-site hardware and move its X86 and IBM POWER technologies to the cloud.
Racksquared is a strong partner and resource for this shift to the cloud. The team has supported Allied to better understand what it takes to move to the cloud and develop the best strategy for them.
“I’ll be able to sleep better at night, and that’s not just because of the cloud,” said Jeff. “It’s also because of Racksquared’s staff and their expertise and responsiveness. They work with us for what we need and change with us as our needs change. I have nothing but good things to say about Racksquared. I would recommend them to anyone.”
Learn more about how Racksquared can support your business.
Visit www.racksquared.com, contact us at sales@racksquared.com or call (855) 380-7225.